Overview
Barber-Nichols, a custom turbomachinery company, is further enhancing their physics-based modeling capability of later generation air foil bearing behavior using Finite Element Analysis (FEA).
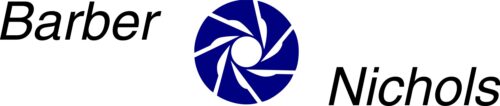
Challenge
Barber-Nichols’ previous air foil bearing design tool was developed for early generations of foil bearings which employed relatively basic, uniform geometries. Although Barber-Nichols has successfully deployed later generation foil bearings in the past, they required the use of a tool that could more quickly predict foil deformation, pressure generation, and film thickness of non-uniform foil geometries. They sought a multiphysics solution that would combine structural and hydrodynamic analyses.
At-A-Glance
Technology Used
- Fluid-structure interaction (FSI) analysis
Challenge
- Model foil bearing behavior
Benefits
- Efficient Design Process
- Expert Support and Knowledge Transfer
- Seamless Integration
Solution
Barber-Nichols turned to SimuTech Group for assistance, seeking their expertise in advanced simulation software, particularly Ansys. SimuTech’s specialists in fluid-structure interaction (FSI) analysis provided invaluable mentorship and technical support, guiding Barber-Nichols through the setup and execution of their first FSI analysis using Ansys tools. This collaboration allowed Barber-Nichols to leverage SimuTech’s extensive experience and knowledge, effectively combining their independent structural and hydrodynamic analyses into a cohesive FSI model.
The Benefits
- Efficiency: With SimuTech’s assistance Barber-Nichols was able to increase their efficiency of solve time, they achieved a 4x improvement, showcasing a significant reduction in time and effort.
- Knowledge Transfer: Mentoring sessions with SimuTech not only provided a solution to the immediate problem but also empowered Barber-Nichols’ engineers with the knowledge and confidence to evaluate other tools and similar analyses for future gains in other technologies.
- Expertise Utilization: By collaborating with SimuTech, Barber-Nichols could tap into a wealth of expertise, ensuring the project’s success and enhancing their own capabilities in advanced simulation techniques.
- Seamless Integration: The seamless collaboration between Barber-Nichols and SimuTech led to an efficient and effective solution air foil design, ultimately strengthening their relationship and laying the groundwork for future partnerships.
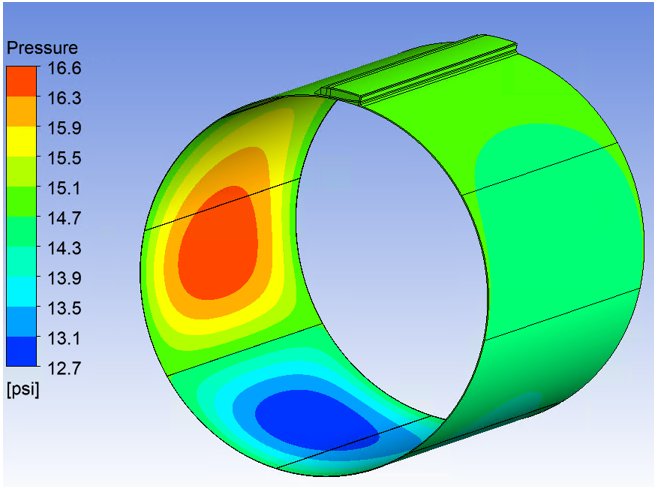
Barber-Nichols’ collaboration with SimuTech Group and Ansys transformed a complex challenge into a manageable solution, delivering significant time savings, enhanced capabilities, and a successful outcome.
Optimize Your Workflow with Industry Leading Solutions
At SimuTech Group, we specialize in bridging the gap between design and reality. Using the most advanced simulation software available, we can predict and optimize critical factors before physical implementation, reducing time-to-market and minimizing costs associated with iterative testing.