Overview
General Fusion‘s mission is to transform the world’s energy supply by bringing zero-carbon fusion power to the grid by the early to mid-2030s. Their approach centers around Magnetized Target Fusion (MTF) technology which aims to harness electricity from fusion reactions. Fusion is the ultimate clean energy solution. It is what powers the sun and stars. General Fusion is working to bring this zero-carbon energy source to Earth with its practical technology.
They embarked on a rapid experimental campaign to scale up for their new fusion demonstration machine called Lawson Machine 26 (LM26).
At-A-Glance
Technology Used
- Ansys LS-Dyna
Challenge
- Scale up a new fusion demonstration machine and overcome complex multiphysics challenges in fusion technology
Outcomes
- Accurate Simulations
- Efficiency Improvements
- Rapid Prototype Development
- Weekly Shot Recommendations
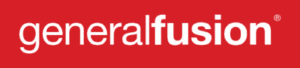
The goal was to validate numerical tools and build confidence in them through a ring compressor test campaign. Collaborating with SimuTech Group and utilizing Ansys LS-Dyna™, General Fusion navigated complex multiphysics problems, significantly advancing their fusion technology.
The results of the campaign were presented at the 2024 American Society of Mechanical Engineers’ Pressure Vessels & Piping® Conference (ASME PVP 2024) in Bellevue, Washington.
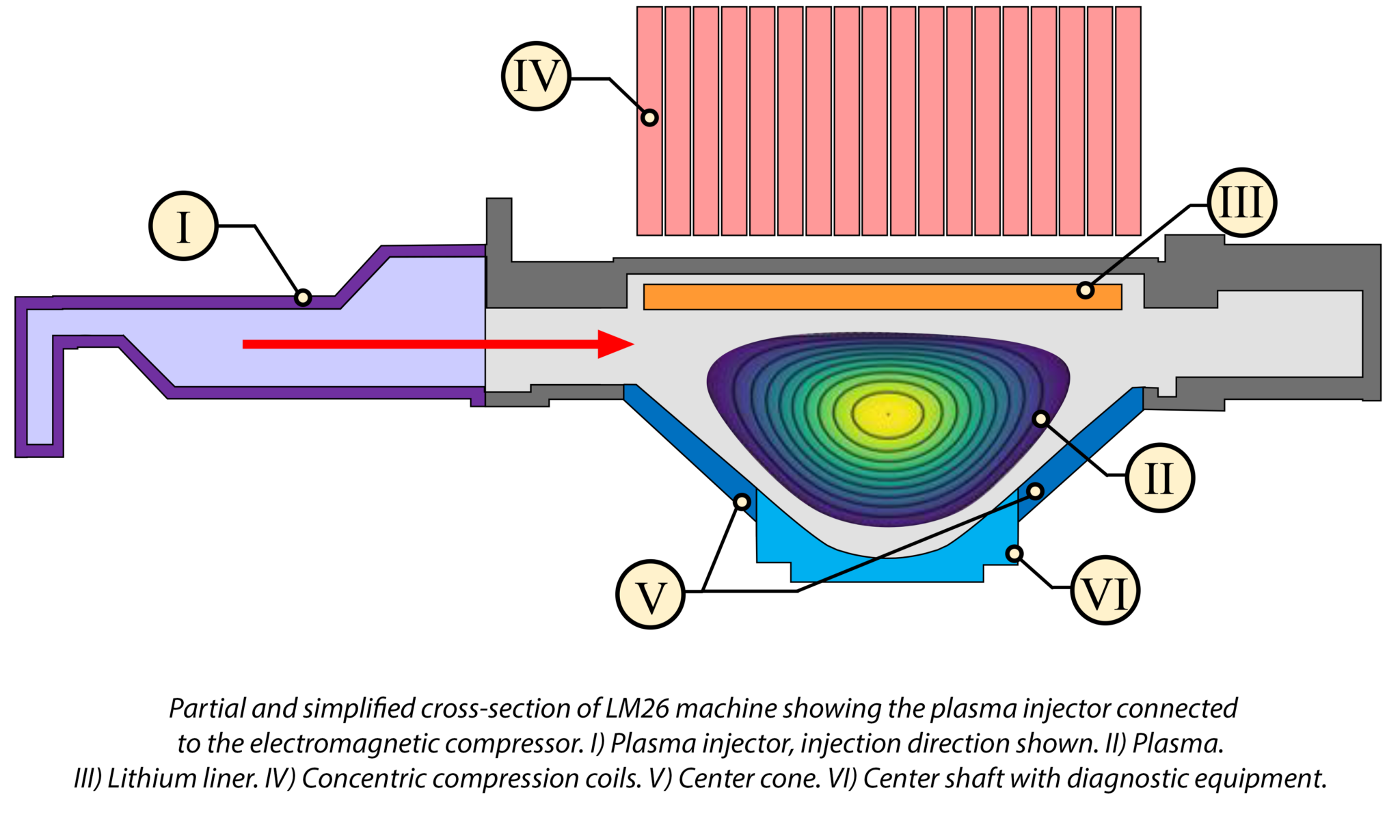
Challenge
General Fusion faced several challenges in their endeavor:
- Complex Multiphysics Problem: The primary challenge was modeling the electromagnetic compression of a solid lithium ring, a complex multiphysics problem requiring accurate simulations.
- Simulation Debugging: The 2D-axisymmetric simulations in Ansys LS-Dyna needed extensive debugging to set up geometry and necessary keywords to run with the electromagnetic solver.
- Material Data Limitations: There was limited data on solid lithium at high strain and strain rates expected in the ring compressor, necessitating customized material models based on in-house tests.
Outcomes
The collaboration with SimuTech and the use of advanced Ansys simulation tools resulted in several positive outcomes:
- Accurate Simulations: Simulations were able to recover test measurements (trajectories, currents, B-fields) within 5-10%, an impressive outcome given the uncertainties in material properties and other measurements.
- Efficiency Improvements: The new axi-symmetric workflow reduced setup time from 10-30 minutes to mere minutes, significantly improving efficiency for simulating larger machines.
- Rapid Prototype Development: The ring compressor test campaign results enabled the quick design and startup of Prototype 0 (P0), a small-scale version of the LM26 compression system, providing critical data and significantly de-risking LM26.
- Weekly Shot Recommendations: The modeling team facilitated a weekly operating rhythm on P0, making shot recommendations that guided the team to achieve the desired performance and loads on the machine.
In the summer of 2023, General Fusion achieved symmetrical compression of a solid lithium ring – the first major project milestone for their new LM26 fusion machine and a necessary step to scaling up for the full-scale compression system.
General Fusion’s partnership with SimuTech Group and the use of LS-Dyna and Electromagnetics solvers for modeling complex multi-physics problems proved to be a pivotal strategy in advancing their fusion technology. The successful ring compressor test campaign and the rapid development of Prototype 0 highlighted the effectiveness of accurate simulations and expert collaborations in overcoming technical challenges. As a result, General Fusion is well-positioned to achieve their goals with the LM26 fusion demonstration machine, thanks to the robust solutions and support provided by SimuTech and Ansys technologies.
Validate Your Project with Industry Leading Solutions
At SimuTech Group, we specialize in bridging the gap between design and reality. Using the most advanced simulation software available, we can predict and optimize critical factors before physical implementation, reducing time-to-market and minimizing costs associated with iterative testing.