Leaders in Aerospace Simulation
The aerospace industry is advancing rapidly, with rising demands for safer, lighter, and more sustainable systems —delivered faster and on tighter budgets. Simulation empowers engineers to accelerate design, reduce physical testing, and meet strict certification standards with confidence.
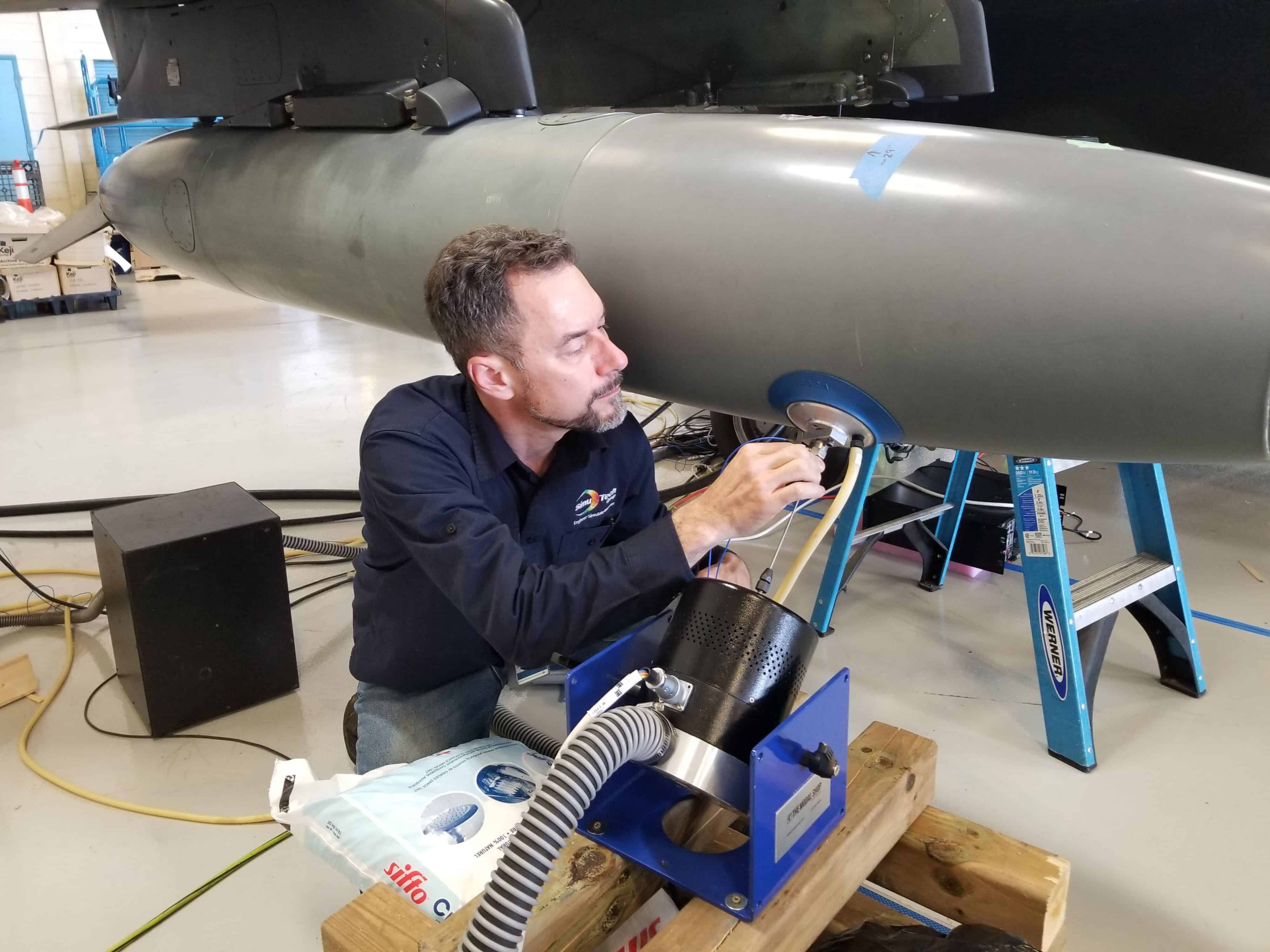
SimuTech supports aerospace teams across propulsion, energy storage, structures, and thermal systems. With powerful simulation tools, expert guidance, and 40+ years of experience, we help solve complex challenges and drive innovation across commercial, defense, and space applications.
Contact Us For Aerospace Simulation Software and Consulting Services
Our Aerospace Project Portfolio
Our aerospace engineering portfolio showcases a diverse range of advanced analysis and design projects, supporting both commercial and defense aviation systems with precision, innovation, and deep technical expertise.
- Acceleration and pressure analysis of titanium potable water tanks on Boeing aircraft
- Stress (proof, burst, HCF, LCF) analysis of exhaust components on Sikorsky helicopters
- Dynamic analysis of a heads-up display on Boeing aircraft
- Fatigue analysis of Flexible and V-band clamps
- Structural analysis of 777X Engine Anti-Ice System
- Mechanism analysis of F-15 landing gear to determine both extension/retraction and joint loads
- Fatigue analysis of F-15 landing gear to determine cycles to failure based on mechanism analysis
- Airworthiness analysis of engine systems
- Mach 5 rocket nozzle steering design
- Thrust and flow analysis of a space shuttle rocket engine with steering from eccentric drag caused by variable chamber impingement
- Supersonic design study of various wing profiles, various angles of attack, and altitude
- Pre-stressed PSD random vibration of electronics PCB assembly
- Fuel coupling piping fatigue analysis
- Development of programs for automation of jet engine simulations
- Advanced mesh-development for engine component thermal/structural analysis
Recent Aerospace Consulting Projects
- Design and analysis of nozzles, afterburner, and external components for both military and commercial engines (F100, F119, F135)
- High cycle fatigue analysis using both random (PSD) and sinusoidal inputs
- Low cycle fatigue analysis of aerospace components including engine and wing anti-ice systems, turbine exhaust cooling ducts, and landing gear
- Engine component qualification testing per RTCA-D0-160D
- Gas turbine blade testing
- Modal testing fields
Aerospace Testing Services
- Ground vibration testing
- Flutter analysis support
- Strain measurements
- Turbine blade testing
- Supplemental Type Certificate Testing (STC Testing)
- Parts Manufacture Approval Testing (PMA testing)
- Aerospace engineering testing services
Common Aerospace Simulation Consulting Topics
Aerostructures
- External Aerodynamics
- Advanced turbulence and transition modeling
- Best-in-class meshing
- Perforations and impacts
- Welding and riveting
- Fatigue
- Fluid-structure interaction
- One- and two-way interaction
- Aeroelasticity analysis
- Metallic and composite materials
- Weight and mass control
- Welding, riveting, bonding
- Mechanical systems
- Safety systems
- Oxygen delivery
- Exits
- Slides
Auxiliary Power Units
- Complete Turbo System
- LP and HP compressors
- Combustion chamber
- HP and LP turbines
- Installations
- Alternators
- Inlets
- Core-compartment
- Leaks and fire extinction
- Fixings and attachments
- Multi-Disciplinary
- Stress
- Thermal
- CFD
- Emag
- Combustion
- Rotordynamics
- Blade Shedding
Cabin & Cockpit
- Air conditioning
- Natural, mixed, and forced convection
- Comfort indices, PPD, PMV (ISO 7730)
- Humidity
- Solar loading
- Seating arrangements
- Locking system
- Stress prediction
- Belts
- Fatigue
- Overhead compartment
- Durability and fatigue
- Openings
- Modal analysis
Electronics
- Avionics Cooling
- Conjugate heat transfer
- Thermal stress
- Modal Analysis
- Random vibration
- Drop test
- Pre-stressed modal analysis
- Safety and durability
- Impacts
- Perforation
- Rack assemblies
- Stress
- Fatigue
- EM Interference
- High and low frequency
Engine Design
- Complete turbo systems
- Fans
- LP and HP compressors
- Combustion chambers
- HP and LP turbines
- Installations
- Mixers and chevrons
- Inlets
- Core-compartment
- Leaks and fire extinction
- Fixings and attachments
- Multi-disciplinary
- Stress
- Thermal
- CFD
- Combustion
Flaps & High Lift Devices
- Performance
- Lift, drag, weight
- Transients
- Moving and deforming bodies
- One- and two-way fluid-structure interactions
- Multibody flexible dynamics
- Acoustics
- Modal analysis
- External CAE couplings
- Structures
- Stress and deformations
- Axis and bearings
- Fatigue
Fuel, Air & Hydraulics
- Multi-purpose
- Valves, pipes, ducts, tanks
- Bleed
- Compressor lines
- Filters
- Mixing
- Air, skydrol, fuel
- Optimization
- Fully parametrized process
- Design of experiments
- Design for Six Sigma
- CAD integration and connectivity
- Workbench bi-directional connectivity
- FLUENT for Catia V5
- Fluid structure interaction
- One-way stresses and deformations
- Two-way moving and deforming bodies
- Multibody flexible dynamics
- Multiscale modeling
- 1D software couplings
Landing Gears
- Acoustics
- Flow
- Mechanical systems
- Multibody flexible dynamics
- Stress and deformation
- Braking systems
- Thermal transients
- Tires
- Deformation
- Explosion and perforation
- Perforations and impacts
- Welding and riveting
- Fatigue
- Fluid-structure interaction
- One- and two-way interaction
- Aeroelasticity analysis
- Anti-icing systems
- Fuel tanks
Nacelle
- Pylon design
- Stress and deformations
- Fatigue
- Vibrations
- Mechanical systems
- Impacts and perforations
- Core-compartment
- Thermal environment
- Ventilation
- Fire extinction
- External shape
- Inlet
- External aerodynamics
- Aeroacoustics
- Mixer and chevrons
- Icing
- Rotordynamics
- Bird strikes and blade shedding
We’re Here to Help
Our team of experienced engineers can assist you at any step of your process.