SimuTech Group has significant experience in applying the following industry and military standards to the solution of complex engineering problems.
Industry Standards
- ASME Boiler & Pressure Vessel Code (BPVC) Section VIII Division 2 and Division 3
- We have assisted customers with both mentoring and consulting project execution using the ASME BPVC.
- Section VIII Division 2 Part 5, Design by Analysis, is the most commonly used method.
- We also have significant experience with high-pressure vessels per Section VIII Division 3.
- ASCE 7-16: Minimum Design Loads for Buildings and Other Structures
- Seismic loads and wind loads are derived for application in a structural analysis, with the ASME BPVC referencing this widely used document.
- BS 7608: Code of Practice for Fatigue Design and Assessment of Steel Structures
- SimuTech has considerable experience applying the methods of BS 7608 towards the evaluation of welded steel structures for fatigue.
- AWS D1.1, D1.6, D1.9: Structural Welding Code for Steel, Stainless Steel, and Titanium
- SimuTech Group also has experience with these AWS welding codes in the evaluation of welded structures for fatigue.
- IIW 1823-07: Recommendations for Fatigue Design of Welded Joints and Components
- ISO 12117-2: Rollover Protective Structures (ROPS) for Excavators of Over 6 tons
- MMPDS: Metallic Materials Properties Development and Standardization
- This is the standard material properties reference for any projects involving the defense and aerospace industries.
Speak to an Expert Today

Military Standards
- MIL-STD-810: Department of Defense Test Method Standard – Environmental Engineering Considerations and Laboratory Tests
- SimuTech Group has significant experience applying the requirements of MIL-STD-810 in the solution of complex dynamic engineering problems.
- The dynamic analysis methods applied include shock (both shock response spectrum and transient shock), random vibration, and sine-on-random/random-on-random.
- MIL-STD-810 considers many different dynamic loading types – an example of over-the-road random vibration input is shown in Figure 514.7C-4.
- MIL-DTL-901: Requirements for Shock Tests, H.I. (High Impact) Shipboard Machinery, Equipment, and Systems (Table XIII)
- For naval shock analysis, SimuTech Group has experience simulating lightweight, medium weight, and heavyweight shock tests using ANSYS.
- Shock inputs typically take the form of a Shock Response Spectrum (SRS).
- SimuTech has methods to transform time-domain shock input to the frequency domain.
- MIL-STD-167: Department of Defense Test Method Standard – Mechanical Vibrations of Shipboard Equipment (Type I – Environmental and Type II – Internally Excited)
- This standard dictates sinusoidal vibration inputs for ship mounted equipment and takes the form of a harmonic response analysis in ANSYS.
- NRL Memorandum Report 1396: Interim Design Values for Shock Design of Shipboard Equipment
- Uses the Dynamic Design Analysis Method (DDAM) capability within ANSYS
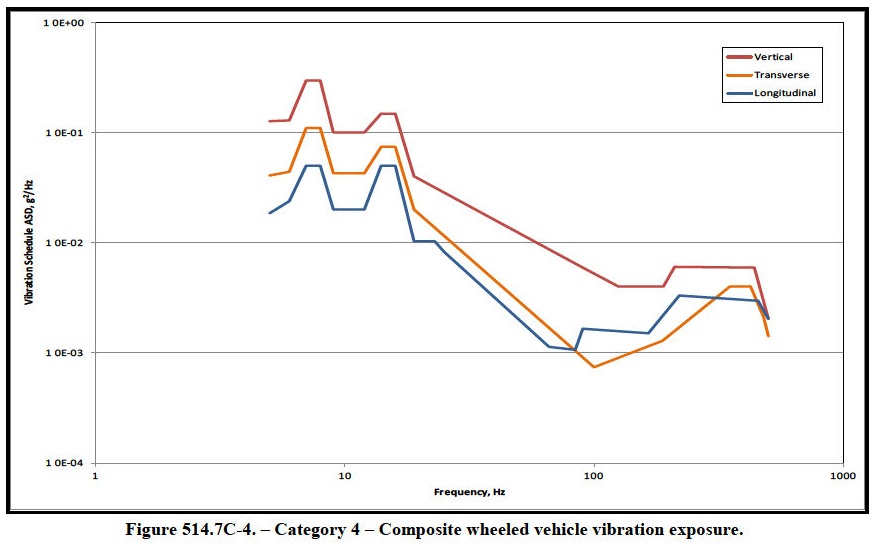
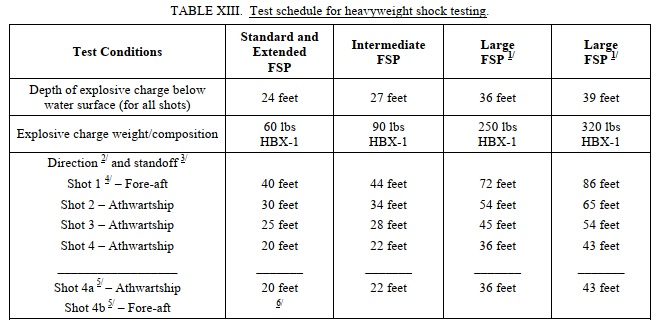
Recent FEA Consulting Projects Where Evaluation per Industry/Military Standards was Necessary
Railcar Pantograph Under Static and Dynamic Loading
The pantograph was simulated under applied static loads as well as random vibration and shock loads along multiple axes, per IEC 61373.
Transportable Radar System Simulated Under Multiple Environmental Operating Conditions
The transportable radar system assembly was evaluated under static and dynamic loading conditions including vibration and shock loading per MIL-STD-810H. Fatigue calculations were carried out for selected load cases.
Analysis of a Pressure Vessel per ASME Section VIII
The vessel was analyzed for primary loads using elastic material properties. An elastic-plastic collapse assessment and a ratcheting assessment were also performed per ASME Section VIII, Division II.
Analysis of a Dynamometer Test Stand for Railcar Chassis Hardware
The test stand assembly was analyzed for static operating loads as well as seismic response loading per ASCE 7. The scale and mass of the test stand is significant enough that analyzing for seismic loading at its install location was essential.
Analysis of Condenser Vessels per ASME Section VIII
The 2 vessels were subjected to cyclic thermal and pressure loading. An analysis of primary plus secondary stress and an ASME fatigue analysis were completed. The simulations and subsequent calculations were carried out per ASME Section VIII, Division 2.
Dynamic Analysis of a Shipboard Radar System
The radar assembly and mounting structure was evaluated under shock and harmonic response loading per MIL-S-901E and MIL-STD-167.
Harnessing FE Simulations for Confident, Standards-Driven Product Development
SimuTech Group engineers regularly perform analyses following the standards outlined above. In many cases, the insights gained through finite element (FE) simulations are invaluable and challenging to replicate with physical testing or traditional hand calculations. These simulations enable our customers to develop new products more efficiently and confidently, ensuring performance meets prescribed standards before physical production begins. Contact us today to get started!
We’re Here to Help
Our team of experienced engineers can assist you at any step of your process.