New Feature Preserves Geometry in Ansys Mechanical Release
In engineering simulation, ‘meshing’ is the process of dividing a complex geometry or domain into a collection of smaller, simpler elements called mesh or grid. The mesh is a mathematical representation of the physical model and introduces some error into the results of the simulation.
Engineers running simulations commonly use a process called mesh convergence or grid independence studies to minimize potential error. Typically, this has been a manual process where the engineer runs an initial simulation with a relatively coarse mesh, manually refines the mesh in regions with large gradients in the results, re-runs the simulation, evaluates the percentage of change in the results in those refined mesh regions and repeats this process until the percent delta in the results is under some small limit (typically 2-5%). Geometry-Preserving Mesh Adaptivity (GPAD) automates this process.
Geometry-Preserving Mesh Adaptivity (GPAD) helps take the guesswork out of mesh sizing
Designers often work with complex models that they are not familiar with or do not have a prior knowledge of critical stress and strain locations. A ‘critical location’ could be holes, fillets, welds, etc. In the case of fluids, the curvature of a surface can affect flow behavior.
In general, there are two methods to approach such situations:
- Generate a coarser mesh, solve the model, and add refinement to areas of importance.
- Generate an overrefined mesh from the start to accurately capture the areas of importance.
Both methods are time consuming and take precious time away from the concept design stage. But, Ansys has released a new feature in the 2023R1 Mechanical release to improve efficiency of durability studies. This new feature, geometry-preserving mesh adaptivity (GPAD), eliminates the need for an overrefined initial mesh and reduces any guesswork needed on mesh sizing.
How Does the GPAD Feature Work?
GPAD enables the designer to start the simulation with an initial coarse mesh. As the model is solved, the solver automatically monitors stress variations in different regions and systematically refines the mesh. The feature is completely automatic and does not require any user input during the solution phase.
It acts as a remesh controller based on certain criteria. Those criteria determine whether the mesh requires modification and, if so, which parts need to be modified. The mesh refinement is based on the underlying CAD geometry—not the initial coarse mesh. The advantage of this is that the mesh refinement works closer to the true shape of the model.
Benefits of GPAD in Mechanical
-
Improved accuracy:
By preserving geometric features, utilizing GPAD can improve the accuracy of structural mechanics simulations. This is especially important in simulations where detailed geometry of the system plays a critical role in determining its physical behavior.
-
Increased efficiency:
Mesh adaptivity can optimize the mesh resolution in regions of interest, thus reducing the computational cost of simulations while maintaining accuracy. This significantly reduces the time and resources required to perform simulations, making it possible to explore more complex and larger-scale problems.
-
Robustness:
GPAD can help ensure robust and stable simulations, even in the presence of highly nonlinear and complex behavior. Because GPAD preserves the geometric features critical to the physical behavior of the system, it provides a more accurate representation of the problem.
-
Flexibility:
Mesh adaptivity can be used to adapt the mesh to different levels of resolution in different parts of the domain, enabling simulations to be tailored to specific requirements or areas of interest. This provides greater flexibility and control over the simulation process and can help identify and isolate specific features of interest.
GPAD Applied
The below design component starts with an initial coarse mesh in all the areas. As the simulation progresses, critical areas such as holes, fillets, chamfers are automatically refined. At the end of the simulation, the results are available on the fine mesh with no need for additional mesh convergence runs.
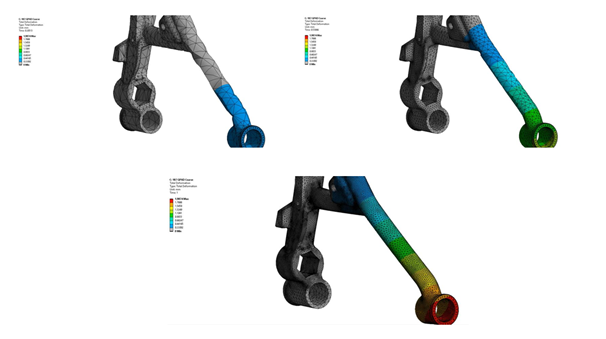
As with any new feature, GPAD does have some limitations which may be addressed in future releases. Some of the limitations include: inability to be used with large deflection analysis, supports only tetrahedral meshes, niche material models such as concrete, shape memory alloy and cast iron are not supported. Large deflection analysis is supported with the existing NLAD (mesh nonlinear adaptivity) capability within Mechanical.
The geometry-preserving mesh adaptivity feature eliminates the need for an overrefined initial meshes or time-consuming manual mesh convergence studies, thereby reducing analysis time while improving efficiency of structural simulations. Engineers spend less time refining meshes and more time optimizing their designs, leading to accelerated time to market and more robust product designs. An example shown above demonstrates the use of GPAD and automatic meshing in a typical structural component.
When used to its full potential, Ansys’ leading-edge simulation software enables creative and ground-breaking product development. Our paid Ansys training courses can accelerate your learning, sharpen your abilities, and help you stay current with the latest technologies, like GPAD in Ansys Mechanical.