Ansys Additive Manufacturing Workflow | Core Enhancements
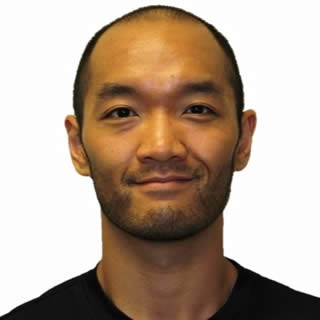
Primary Additive Mfg Engineer
Ansys Additive Manufacturing (AM) workflow joins materials to make objects from 3D model data, usually layer upon layer (ASTM F2792). In this way, AM allows levels of hierarchical, shape, material and functional complexities unequaled by conventional manufacturing technologies.
Metal/Mining Additive Manufacturing (AM) Growth
In the metal industry, AM successes are many:
Aviation: GE 3D-printed their 30,000th fuel nozzle tip for their LEAP engine in October 2018. Better fuel efficiency, weight reduction, and part consolidation were some of the benefits of using additive technologies;
Biomedical: Stryker offers implants integrating their Tritanium® In-Growth Technology, which features an additively manufactured porous structure that promotes bone in-growth and biological fixation;
Aerospace: Relativity Space has built Stargate, the largest metal 3D printer in the world that will be used to produce entirely 3D-printed rockets in a matter days instead of years;
Dental: 3DRPD has 3D-printed over 150,000 patient-specific removable partial dentures made of biocompatible cobalt-chrome alloy using the laser powder bed fusion process.
With the continuous interest around metal AM, industry needs are growing–and becoming more rigorous and complex. Research centers may want to develop a new recipe (i.e., change the manufacturing process parameters) to print a metal that does not exist yet, and companies that own multiple 3D printers may want to make sure their machines will not stop due to manufacturing-related issues. To fulfill this increasing demand, a virtual testing environment offered by simulation can be of benefit. To this end, early in 2018, Ansys created a complete design-to-print solution for the entire AM process chain with a focus on laser powder bed fusion (LPBF) technology.
Ansys Additive Manufacturing Solutions offers a plentiful of tools for all type of AM users:
- Ansys Additive Print allows direct AM users and machine operators with no FEA background to simulate the LPBF process in order to find the optimal orientation for their part based on different criterion: part distortion, residual stress, build time, and support materials.
- Ansys Workbench Additive allows AM designers and analysts to design a part based on the various Ansys optimization tools, perform part validation, and simulate the LPBF process within a self-contained Workbench project enabling parametric studies.
- Ansys Additive Science allows material scientists and researchers to have a scientific and fundamental understanding on the LPBF process. Prediction of the melt pool dimensions, porosity, microstructure, layer-by-layer thermal history, track phase transformation is part of the capabilities of this tool.
Experimental Validation | Ansys Additive Manufacturing Workflow
Finally, because these tools are so new, not many experimental validation studies have been published in the literature so far. Therefore, to strengthen our confidence in these simulation tools, SimuTech Group and École de technologie supérieure (a public engineering school in Montreal, Quebec, Canada) have partnered on an experimental validation of the distortion prediction capability of Ansys Additive Print.
While this study is still underway, preliminary results indicate good agreement between the experimental and numerical measurements. The outcome of this project has been and will be presented at various events in 2019: CASI AERO 2019 Conference, NSERC HI-AM Conference 2019, NAFEMS World Congress 2019 and Additive Manufacturing Conference and Expo 2019.
For more details, please consult our Tips and Tricks in SimuTech Skills Center, where introductions and tutorials are available for these tools.
Additional Ansys Software Tips & Tricks Resources
- For guidance on Pre-Stressed Modal Analysis Linked to Nonlinear Static Analysis
- For support on Compiling and Loading User Defined Functions (UDFs)
- For Extreme Thermal Expansion Modeling in Mechanical
- For enhancing Autonomous Vehicle Hazard Recognition
- For advanced Analysis of Models Exhibiting Cyclic Symmetry
- Deploying *TREAD in Mechanical APDL to Read External Data
- For Replicating Base Acceleration in Harmonic Analysis