Ansys Webinar Description:
Ansys Fluent Watertight Geometry Workflow directs users through a step-by-step process of simple, intuitive inputs.
Fluent Meshing Watertight and Fault Tolerant Workflows
In addition, this utility makes it possible to take advantage of the full single window workflow in Fluent, from geometry import to meshing to solving and post-processing.
Fault Tolerant Workflow quickly wraps and seals leaks and gaps in complex and dirty geometries. Moreover, parallel poly-hexcore (Mosaic) technology is now available for both workflows. This expanded features allows users to create high quality mesh grids for complex geometries faster than ever.
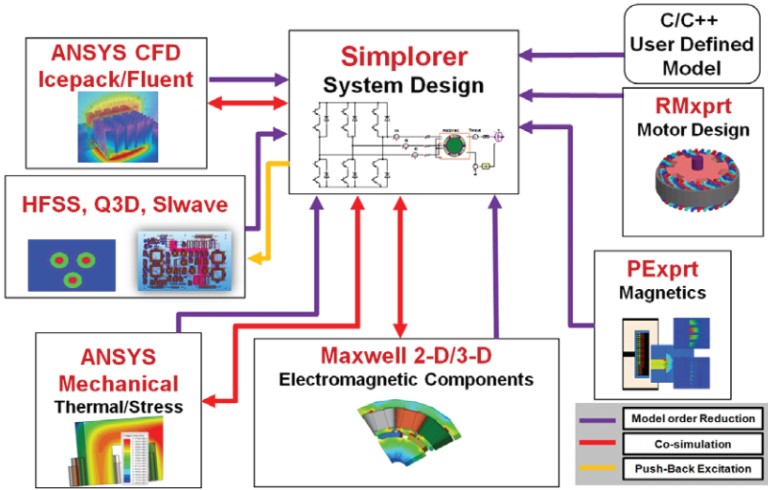
Task-based Meshing Workflow with Watertight CFD Geometry
So, you want to increase productivity through watertight geometry workflow meshing? You’re in the right place.
In short, your productivity will increase with the help of new Watertight Geometry Workflow Meshing features in Ansys Fluent.
Additionally, completing the task-based workflow is simple if you start with a reasonably simple model. You are given a number of options, including:
- Import of CAD.
- Surface Meshing
- Defining Geometry
- Model Capping
- Volumetric Flow Extraction
- Meshing at Volume
By selecting “Switch-to-Solution,” you may now bring the mesh up in the well-known Fluent interface.
What happens, though, if you want to replicate a more complex model, such as air cooling an electric motor? Let’s look at some watertight geometry workflow hints and tips to quickly pre-process this complicated model.
Flow Volume Transfer from Ansys SpaceClaim to Ansys Fluent
Using Ansys Fluent’s capping tools to create an internal flow volume will make extraction simple.
Ansys SpaceClaim requires the creation of an exterior flow boundary in order to simulate external flows, such as the airflow cooling a motor.
Ansys Share Topology Feature
Draw a cube around the motor to accomplish this, and then use the Share Topology feature.
Share Topology merges into a single face all faces that overlap between two solids. Additionally, it resolves the point at which any motor component intersects with the cube. ST additionally defines flow regions that do not involve Boolean operations.
With Fluent’s Surface Mesh operation, the flow volume will be extracted. The volume will resemble the space between the cube’s and the motor’s edges.
Why You Should Name the Entities in Your Model in SpaceClaim
There are a few additional SpaceClaim tips and tactics that you can use when working on your geometry that may come in handy later on.
First, add the word “fluid” to the cube’s name that surrounds the motor geometry. That will cause the watertight geometry workflow to recognize it as a fluid region automatically.
Create a practice of adding evocative strings to the names of other entities, like as
- Inlets & Outlets.
- Planes of Symmetry
Fluent will know to define these entities as inlets, outlets, symmetry planes, and more if you include these strings in the entity name. This will make your Ansys Fluent Watertight Geometry Workflows super easy.
And voila, the motor model can now be imported into Fluent!
Additional Engineering Webinars
- Performing Bolt Pre-Tension Analysis
- Engineering Testing vs Simulation Analysis
- FEA-based Weld Fatigue Analysis
- Stress Linearization for ASME Boiler & Pressure Vessel Code
- Random Vibration Analysis (PSD) in Mechanical
- Shared Topology, Verification and Pre-Cracked Mesh