Turbomachinery design is increasingly carried out by means of automated workflows based on high-fidelity physical models. More specifically, employing optimization algorithms concurrent in geometry parametrization.
Currently, parametrization methods used for this purpose are often tailored to one particular type of turbomachinery blade. In this state, not providing shape derivatives required for gradient-based optimization.
Additionally, these methods are not suited to re-parametrize a baseline blade geometry. This baseline, defined by a set of scattered point coordinates in a systematic way.
Here, this research presents a general blade parametrization method for axial, radial, and mixed flow blades based on typical turbomachinery. This includes, design variables, along with NURBS curves and surfaces.
The shape derivatives are computed by means of the complex-step method. In short, enabling the integration of the parametrization into gradient-based shape optimization workflows.
Moreover, this method permits the re-parametrization of a blade geometry defined by a cloud of points by solving a two-step optimization problem. The capabilities of the method are demonstrated by replicating eight blade geometries. That is, in two and three dimensions, with an accuracy comparable to the tolerances of current manufacturing technologies.
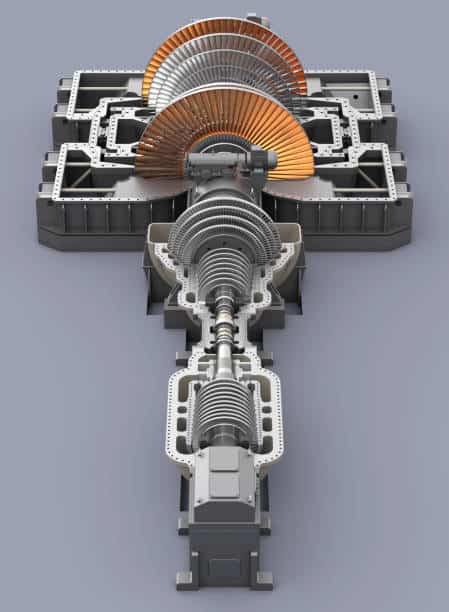
Multi-Objective Optimization |
Mixed Flow Impeller
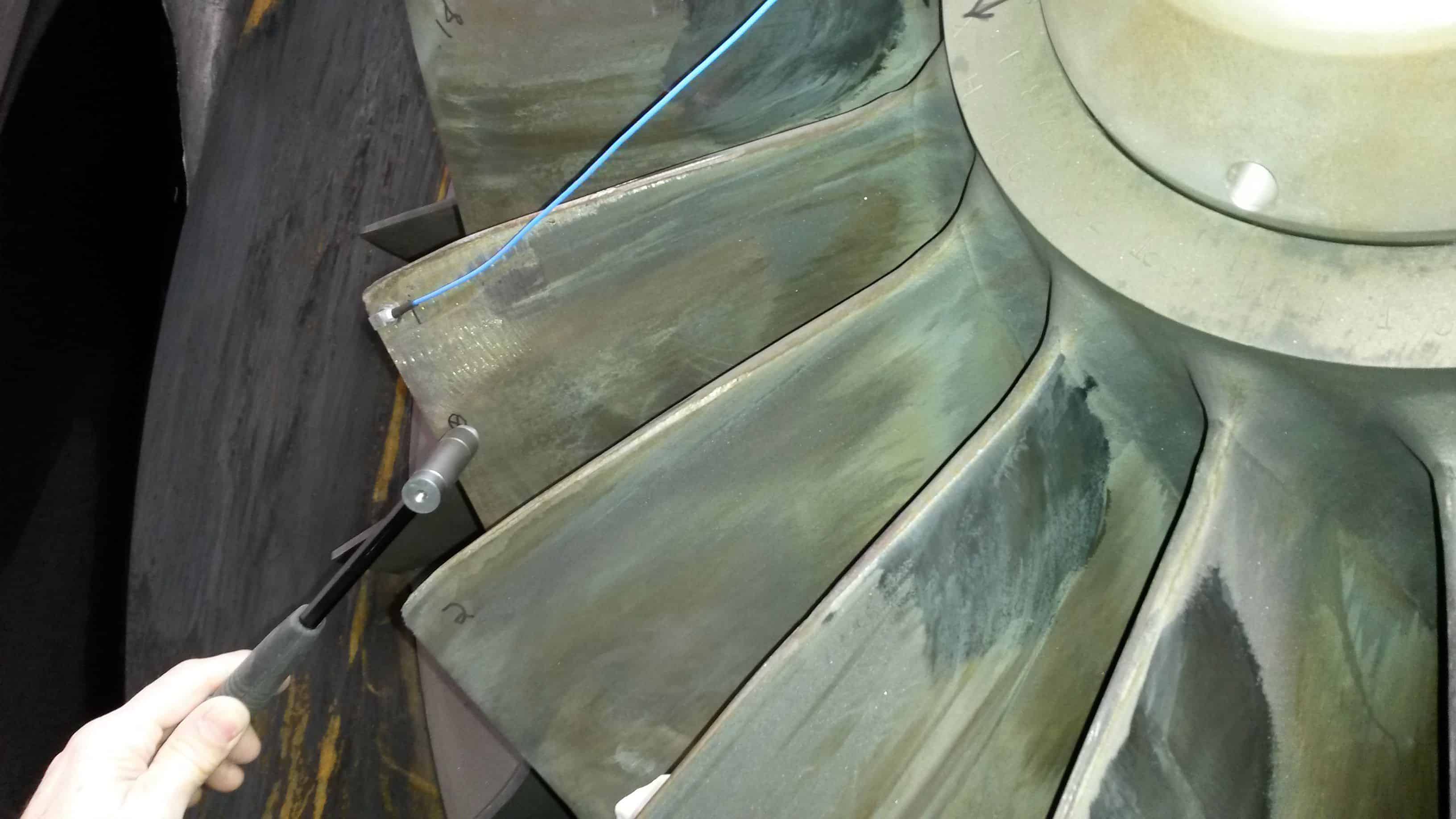
In addition, SimuTech Group engineers test and analyze the effects of blade deformation under running conditions on the performance of a highly loaded transonic mixed flow impeller.
Cyclic Symmetry Analysis |
Turbine Fan Blade Assembly
What’s more, cyclic symmetry analysis enables the efficient assessment of full blade sets in gas or stream turbines. In the video above, our team spotlights Ansys’ software capabilities, providing a blanket overview for cyclic symmetry analysis.
Related Mechanical Testing Services Offered
Campbell Testing
Measuring the natural frequencies and mode shapes of rotating turbine blade (bucket) rows.
Torsional Vibration
Determine the natural frequencies and mode shapes of a rotor train as it twists about the axis of rotation.
Vibration Diagnostics
Identify the root cause of noise and vibration problems in machinery via ODS, spectral, order tracking or joint time frequency analysis.