Designing Reliable, High-Efficiency Energy Systems for Aerospace Applications
In aviation, energy storage systems must be compact, lightweight, and incredibly resilient, managing intense thermal, mechanical, and electrical loads without failure. As electric and hybrid aircraft development accelerates, simulation gives engineers the insight needed to meet rigorous demands for power density, durability, and safety.
Simulation helps you solve the toughest energy challenges in aerospace. Let’s talk about how we can support your battery or fuel cell system from concept to certification.
The Critical Role of Energy Storage in Sustainable Aviation
For all-electric and hybrid-electric propulsion to succeed, energy storage systems must deliver high energy density without compromising reliability. Aircraft require batteries and fuel cells that perform across variable flight conditions, resist vibration, and maintain safe operation even under extreme thermal and electrical stress.
Simulation enables engineers to:
- Model and optimize battery architecture and housing
- Predict electrochemical performance and degradation over time
- Simulate structural response to vibration and pressure fluctuations
- Identify and mitigate thermal runaway and EMI/EMC issues
Request a Consultation
Battery Systems for Aviation
Battery design in aerospace presents a delicate balancing act. Systems must pack significant energy into a tight, lightweight form factor, all while managing heat, vibration, and EMI. With simulation, developers can:
- Predict thermal behavior across duty cycles (Fluent, Icepak)
- Assess structural integrity under aircraft vibration and G-loads
- Simulate discharge and recharge performance (Chemkin)
- Identify failure points in cell packaging or connectors
Fuel Cells and Hydrogen Storage
Hydrogen fuel cells present an alternative to traditional batteries, but they also introduce new challenges like cryogenic storage and flashback risk. Simulation supports:
- Cryogenic tank and valve design for sub-zero durability
- Fuel cell electrochemistry and water management
- Thermal and fluid analysis
- EMI/EMC compliance with high-current fuel cell systems
Power Management and System Integration
Whether using batteries or fuel cells, aerospace engineers must ensure seamless integration with propulsion systems, avionics, and power electronics. Simulation helps manage this complexity by enabling full-system modeling and embedded control software validation. Tools enable:
- Real-time embedded software co-simulation (SCADE)
- System-level EMI/EMC compliance simulation (SIwave, HFSS, EMC Plus)
- Optimization of cabling, busbars, and thermal management
- Tradeoff analysis between energy density, weight, and safety
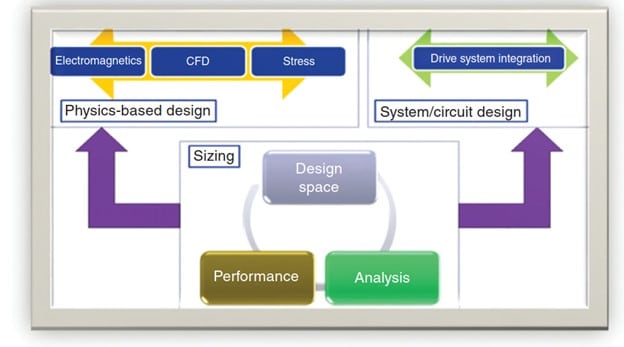
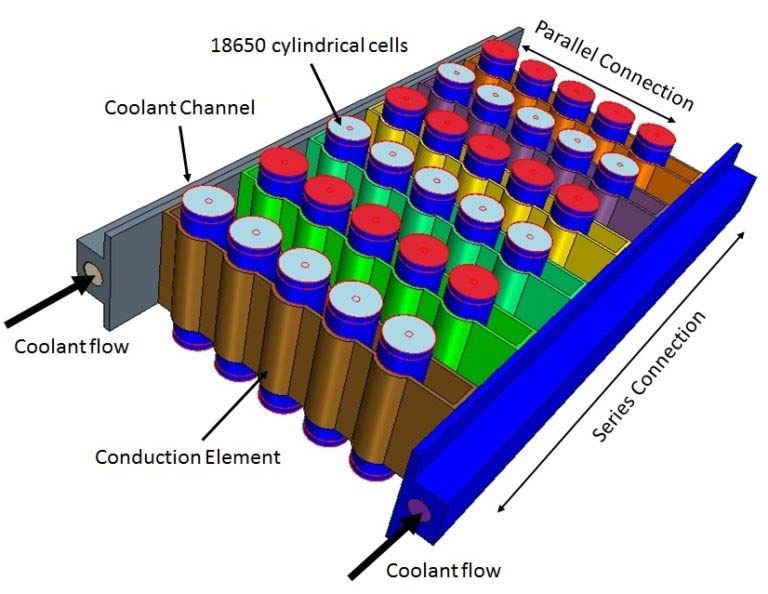
SimuTech’s Simulation Tools for Energy Storage Innovation
We support aerospace development with a full suite of Ansys simulation capabilities:
- Fluent, Icepak, Chemkin – Fluid dynamics, thermal management and electro-chemical performance
- Granta – Materials selection and sustainability profiling
- Maxwell, SIwave, EMC Plus – Electromagnetic analysis and EMI/EMC simulation
- SCADE – Embedded software development for control logic
- Mechanical – Structural performance and vibration durability
Why Work with SimuTech Group?
SimuTech Group helps aerospace engineering teams tackle the complexities of energy storage, from battery durability to fuel cell integration. With 40+ years of aerospace propulsion experience, and as the largest certified Ansys partner in North America, we offer simulation software, consulting, and training to accelerate your energy storage development timeline and enhance safety at every step.
From thermal management to vibration testing, simulation makes safer, more efficient energy storage possible. Talk to SimuTech Group to power your next aerospace project with confidence.
Other Aerospace Industry Applications
We’re Here to Help
Our team of experienced engineers can assist you at any step of your process.